Specjalny, antypoślizgowy lakier dający efekt szorstkiej powierzchni, do metali, tworzyw sztucznych wzmocnionych włóknem szklanym, kompozytów i do drewna. Cykl obejmuje dwa produkty oferujące szerokie możliwości personalizacji i efektów, schnące naturalnie
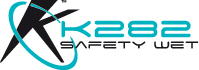
Kolory
Może być produkowany we wszystkich wariantach kolorystycznych, na podstawie międzynarodowych kart kolorów lub wzorca.
Zastosowanie
Od lat stosowany na dużych i małych łodziach do lakierowania mostków i schodów w celu ograniczenia ryzyka poślizgu na mokrych powierzchniach.
Modulowana szorstkość sprawia, iż nadaje się on również do siłowni okrętowych i lokali usługowych, w których istnieje duży ruch pieszych, również w obuwiu.
Główne właściwości
- duża odporność na słońce i zasolenie
- nieprzemakalny dla wody i dla czynników chemicznych
- doskonały środek antykorozyjny dla metali, bardzo odporny na zużycie
Modulowany efekt szorstkości, od delikatnego, przeznaczonego dla bosych stóp, do bardzo szorstkiego do zastosowań technicznych.
Przygotowanie powierzchni przeznaczonych do lakierowania
- Metale: w przypadku powszechnie spotykanych rodzajów stali i aluminium bez gładkiego i lustrzanego wykończenia należy je dobrze wyczyścić w celu usunięcia śladów kurzu i tłuszczu. Jeżeli lakierowane mają być metale trudniejsze, o bardziej błyszczących powierzchniach, dobrze jest wykonać piaskowanie, szlifowanie lub szczotkowanie, aby poprawić właściwości adhezyjne.
- Tworzywa wzmocnione włóknem szklanym i kompozyty: zazwyczaj prawidłowe oczyszczenie podłoża umożliwia idealne warunki adhezji.
- W każdym razie zaleca się piaskowanie, szlifowanie lub szczotkowanie podłoży o zbyt błyszczącej powierzchni.
- Drewno: podkład doskonale przylega do najbardziej popularnych rodzajów obróbki powierzchniowej drewna.
Nakładanie
Oba produkty nakłada się natryskowo, co daje jednakową grubość powłok oraz efekt antypoślizgowy. Podkład pełni funkcję aktywatora adhezji i po wyschnięciu można łatwo nałożyć na niego powłokę wykończeniową.
Nakładanie za pomocą zwykłych urządzeń typu airmix lub airless, dyszami o średnicy od minimalnie 1,5 mm do 2,2 mm, pod ciśnieniem powietrza 3-4 bar.
Aby powłoka wykończeniowa była jednolita, należy nakładać kilka warstw metodą krzyżową. Grubość powłoki końcowej cyklu mieści się w granicach od 60 do 150 mikronów.